はじめに
製造現場では、不良品の流出が大きな問題です。不良率が高いと、コストが増え、顧客の信頼を失いかねません。技術職として、不良率改善に向けた取り組みは避けて通れません。この記事では、実際の現場でどのように不良率改善に取り組んでいるのか、その方法と課題を紹介します。
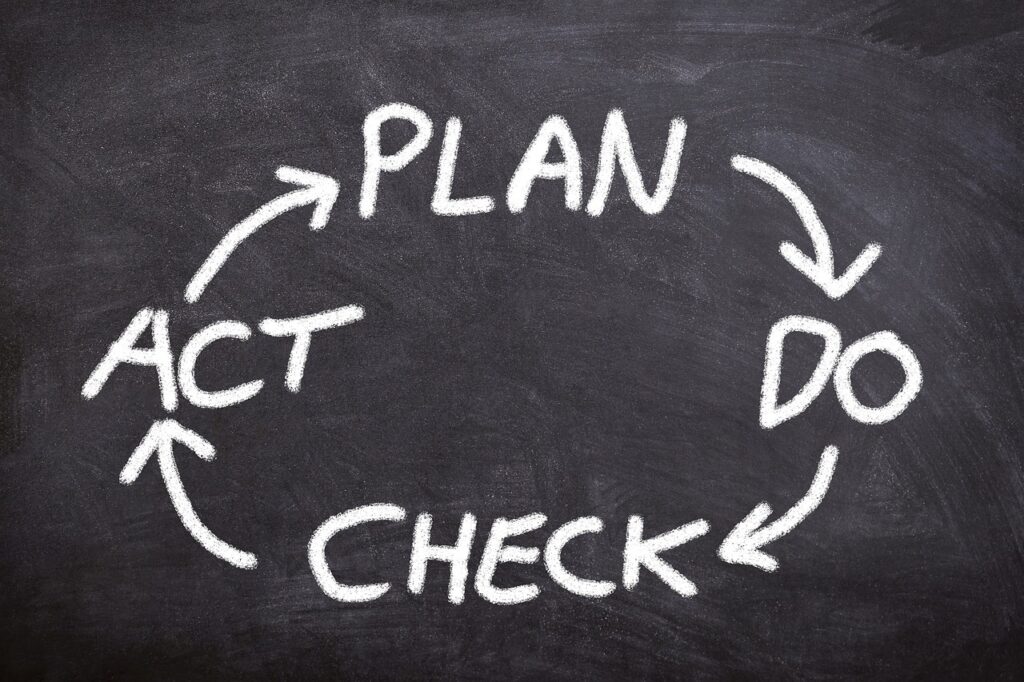
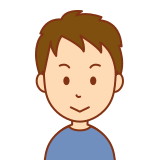
お疲れ様です、先輩!最近、不良率が少し高くなっている気がするんですが…。

うーん、確かに最近ちょっと調子悪いな。特に、部品の精度が落ちてる感じがするな。
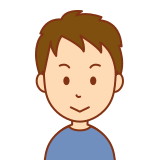
じゃあ、どうすれば良いですか?何か改善策はありますか?

まずは、どこで不良が発生しているのか、データでしっかり確認することが大事だな。現場での実際の原因を突き止めないと、改善策も無駄になっちゃう。
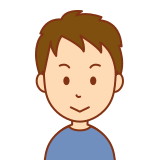
データって、例えば不良品の種類とか、不良が発生したタイミングとかですか?

その通り!例えば、どの工程で不良品が多く出ているか、作業時間帯や作業員ごとの不良率などを集計して分析するんだ。これで、改善が必要な部分が見えてくる。
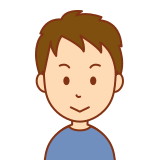
なるほど、データを見て原因を絞り込むんですね。

そうそう。で、その次は、原因に応じて改善策を講じる。例えば、設備の調整が必要なら、早急に保全に頼んで調整してもらうし、作業員の教育が足りないなら、トレーニングを強化する。
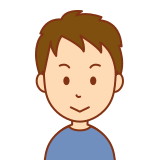
それで、少しでも不良率を下げていくってわけですね。

その通り!でも、改善策を打ったらすぐに結果が出るわけじゃないから、改善後もモニタリングして効果を確認することが重要だよ。
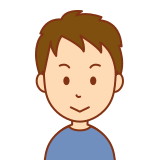
効果の確認ですね。たしかに、改善策が効果を発揮しているかを追わなきゃいけませんね。

その通り。あとは、チーム全体で不良率改善を共有して、みんなで意識を高めることが大事だよ。改善のために全員が協力していけば、結果的に不良率は下がっていくから。
【解決策】
- データ収集と分析
- 不良品が出ている原因を突き止めるためには、データ収集と分析が欠かせません。どの工程で不良が発生しているのか、どの時間帯で問題が多いのかを正確に把握することが第一歩です。集めたデータを基に、効果的な改善策を導き出しましょう。
- 原因に基づいた改善策の実施
- 不良品が出る原因には、機械の設定ミス、部品の不良、作業員の手順ミスなど、さまざまな要因があります。それぞれの原因に応じた改善策を打ち出すことが重要です。例えば、機械の調整や作業手順の見直し、作業員への再教育などが考えられます。
- 改善後の効果の確認
- 改善策を実施した後は、しっかりとモニタリングして、効果が出ているか確認しましょう。もし改善が見られない場合は、再度原因を探り、別のアプローチを検討します。
- チーム全体での意識共有
- 不良率改善は一人でできるものではありません。工場内のチーム全体で協力し、意識を共有することが大切です。みんなで問題意識を持って改善に取り組むことで、より早く効果を得ることができます。
- 継続的な改善活動
- 不良率改善は一回で終わるものではなく、継続的な努力が求められます。定期的にデータを確認し、改善策が効果的に運用されているかをチェックし、必要に応じて次の改善策を講じていきましょう。
さいごに
不良率の改善は、時間がかかることもありますが、着実に結果を出すためには、データに基づいた原因分析と、現場の協力が不可欠です。今回紹介したように、どんな小さな原因でも見逃さず、改善を続けることで、不良率を減らし、品質向上を実現することができます。
愚直にPDCAを回し続けるのが一番の近道です。
改善活動を続けることで、最終的には顧客満足度の向上や、工場の生産性向上にもつながります。技術職として、日々の仕事に真摯に取り組みながら、品質の向上を目指していきましょう!
本一部の紹介ですが、イメージが沸いてきたでしょうか?
コメント